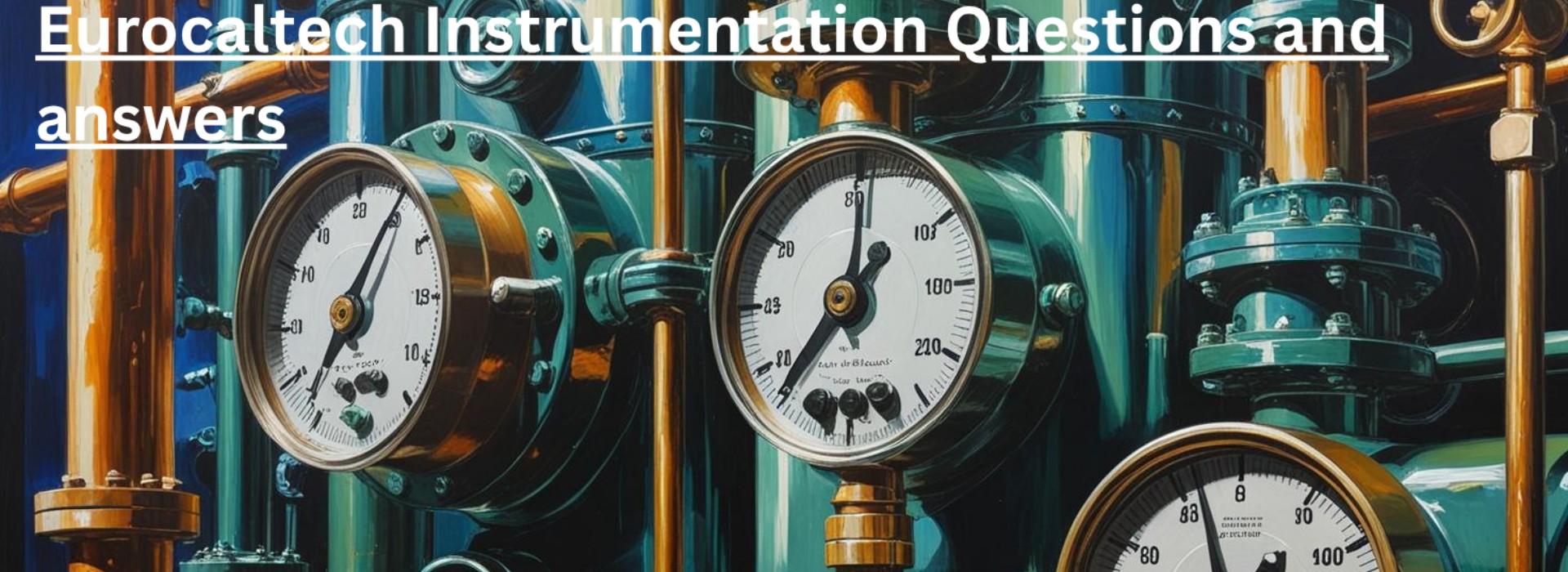
Control Valves instrumentation interview questions and answer
CONTROL
VALVES
A control valve is a final control element that directly changes the valve of a manipulated variable by changing the rate of flow of control agent. It consists of an operator and valve body, with the operator providing power to vary the position of the valve plug inside the body. Common types of control valves include single-seated valves, double-seated valves, and actuators. The valve coefficient (CV) is defined as the number of gallons per minute of water passing through a fully open valve at a pressure drop of 1 psi.
This discusses various valve types, including butterfly, three-way, cage, camflex, link connected to valve positioner, booster relays, angle valves, and solenoid valves. Butterfly valves are used in systems with small pressure drops, while three-way control valves are used in special systems. Plugs include V-port and contoured plugs, cage valves for noise reduction, camflex valves for increased actuator forces, and booster relays for volume boosters, ratio relays, and reversing relays. Angle valves are used for high-pressure drops and severe conditions.
What is a control valves?
A control valve is the final
control element, which directly changes the valve of the manipulated variable
by changing the rate of flow of control agent.
A control valve consists of
an operator and valve body. The operator provides the power to vary the
position of the valve plug inside the body. The plug is connected to the
operator by a stem, which slides through a stuffing box. The air signal from
the controller is applied above the diaphragm. The increasing air signal from
the controller is applied above the diaphragm. An increasing air signal will
push the operator stem downwards against the force exerted by the spring on the
diaphragm plate. The valve is adjusted in such a way that the plug starts
moving when 3 psi is applied to the diaphragm and touches the seat when 15 psi
is applied to the diaphragm. Thus an increase in air pressure will close the
valve. Hence the home "Air to Close". Another type is "Air to
open", such that 3 psi on the diaphragm the value is closed and 15 psi air
signal it in fully open.
90. What
are the different types of control valves?
The commonly used control
valves can be divided as follows.
1. Depending on Action.
2. Depending on the Body.
1. Depending on action:
Depending on action there are two types of control valves, (1) Air to close, (2) Air to
open.
2. Depending on body:
1. Globe
valves single or double seated.
2. Angle
valves.
3. Butterfly
valves.
4. Three
way valves.
5. Ball
valves
91. What
is the use of single seated valve?
The single seated valve is
used on smaller sizes, and in valve of larger sizes, where an absolute shut off
is required. The use of single seated valve is limited by pressure drop across
the valve in the closed or almost closed position.
92. What
is the use of double-seated valve?
In double seated valves the
upward and downward forces on the plug due to reduction of fluid pressure are
nearly equalized. It is generally used on bigger size valves and high-pressure
systems. Actuator forces required are less i.e. a small size actuator.
93. What
is CV of a valve?
Cv is the capacity of a
valve and is defined as:
"No. of gallons per
minute of water which passes through a fully open valve at a pressure drop of 1
psi.
CV =
q ( ?P / G )
Where: Cv = Valve co-efficient
q = Volumetric flow rate
(gallons / minute)
?P = Pressure drop across the valve
in psi.
G = Specific gravity of
flowing fluid.
The valve coefficient Cv is
proportional to the area 'A' between the plug and valve seat measured
perpendicularly to the direction of flow.
94. What are the
different types of actuators?
The different types of
actuators are:
1. Diaphragm
Operated.
2. Piston Operated.
95. What
types of bonnets would you use of high temp? And very low temp. ?
High temperature: Bonnets are
provided with radiation fins to prevent gland packing from getting damaged.
On very low
temperature: Extended bonnets are used to prevent gland packing from getting freeze.
96.
How will you work on a control valve while it is line?
While the control valve is
in line or in service, it has to be by passed and secondly the line to be
depressurized and drained.
97. What
is the use of a valve positioner?
The valve positioner is used
for following reasons:
1. Quick Action control
valve.
2. Valve hysteresis.
3. Valves used on viscous
liquids.
4.
5. Line pressure changes on
valve.
6. Valve Bench set not
standard.
7. Reversing valve operation.
98.
When can a by pass be not used on a positioner?
A by pass on a positioner
cannot be used when:
1.
2. Reverse Acting
Positioner.
3. Valve bench set not
standard.
Butterfly valves are used
only in systems where a small pressure drop across the valve is allowed. The
butterfly is fully open when the disc rotates by 90. A drawback of this
valve is that even a very small angular displacement produces a big change in
flow.
100. What is the use of three way valves?
Three way control valves are
only used on special systems, where a dividing or mixture of flows according to
a controlled ratio is required.
101. What are the different types of plugs?
The different types of plugs
are generally used are:
(1) V.
port plug (2) Contoured plug
V-port plug:
Ported plug are generally used on double-seated valves. This is because
ported plugs, have a more constant off balance area.
Contoured plug:
Contoured plugs are generally used on
single seated valve with small trim sizes.
102. What is a cage valve?
A cage valve uses a piston
with piston ring seal attached to the single seated valve "plug".
Here the hydrostatic forces acting on the top or the piston or below the valve
plug tend to cancel out. The seat ring is clamped in by a cage. Cage valves are
generally used for noise reduction.
103. What are the advantages of Camflex valves?
Camflex valves are
intermediates between globe valve and butterfly valve. The plug rotates 60' for
full opening.
Advantages:
1. Actuator forces required
are very less.
2. Extended bonnet and hence
can be used on any service i.e. on high temperature and very low
temperature.
3. Variations in flow.
4. Light weight.
104. What is the use of link connected to the valve positioner?
The link serves as the feed
back to the value. Ant valve movement is sensed by this link. Sometimes due to
line pressure changes on H.P. service the valve position may be changed, the
link in turn senses this change and the positioner will produce an output which
will operate the valve to the original position.
105. What is the use of booster relays?
Booster relays are
essentially air load, self-contained pressure regulators. They are classified
into three broad groups:
1.
Volume Boosters: These are used to multiply the available volume of
air signal.
2. Ratio
Relays: Use to multiply or divide the pressure of an input signal.
3. Reversing
Relays: This produces a decreasing output signal for an increasing input signal.
106. What is the use of Angle valves?
Angle valves are used where
very high-pressure drops are required and under very severe conditions. Where
the conventional type of valve would be damaged by erosion.
107. What are the different valve characteristics?
The different types of valve
characteristic are:
1. Linear 2. Equal Percentage 3. Quick Opening.
1.
Linear: The valve opening to flow rate is a linear curve
2.
Equal percentage: For equal increments of valve opening it will give
equal increment in flow rate range. At small opening the flow will also be
small.
3.
Quick opening: At small opening the increments in flow rate is
more. At higher opening the flow rate becomes steady.
108. What is a solenoid valve? Where it is used?
A solenoid is electrically
operated valve. It consist of a solenoid (coil) in which a magnetic plunger
moves which is connected to the plug and tends to open or close the value.
There are two types of solenoid valves:
1. Normally open 2. Normally closed
USE: It is used for
safety purpose.
109. How will you change the valve characteristics with positioner?
The positioner contains
different types of cam in it. Selection of the proper cams in it. By selection
of the proper cam the valve opening characteristics can be changed.
110. How will you change the action of a control valve?
1. If the control valve is
without bottom cap.The actual needs to be changed.
2. If bottom cap is
provided.
a) Disconnect the stem from
the actuator stem.
b) Separate the body from
the bonnet.
c) Remove the bottom cap and
the plug from body.
d) Detach the plug from the
stem by removing the pin.
e) Fix the stem at the other
end of the plug and fix the pin back.
f) Turn the body upside
down. Connect it to the bonnet after inserting the plug and stem.
g) Connect back the stem to
the actuator stem.
h) Fix back the bottom cap.
i) Calibrate the valve.
111. How will you select the control valve characteristics?
The graphic display of flow
various lift shows then the Desired or inherent characteristic is changed by
variations pressure drop. This occurs as the process changes from condition
where most of pressure drop takes place at the control valve is a condition
where most of the pressure drop is generally distributed through rest of the
system.
% Flow: This variation in
where most of the total drop take place is one of the most important aspects is
choosing the proper valve characteristics for give process.
Flow control: Normally Equal
percentage valve is used.
Pressure Control: Normally linear
valve is used to maintain a constant pressure drop.
Temp. Control: Normally equal
percentage valve is used.
Liquid Level
Control: Normally linear valve is used.
Basically in selecting a
valve characteristic two important points have to be taken into account.
a) There should be a linear
relationship between the position of the plug and the flow through the valve in
a wide range of change in the pressure drop across the valve.
b) The pressure drop across a valve should be as low as possible.
Control valve sizing
112. What is the effect of pipe reducers on valve capacity?
When control valves are mounted between pipe reducers, there is a
decrease in the actual valve capacity. The reducers create an additional
pressure drop in the system by acting as contractions of enlargements in series
with the valve.
Metric formula: for inlet
and outlet reduces.
2
d2 Cv2
R =
1 – 1.5 1 -
D2 0.04d2
For outlet reducer only or inlet reducer with entrance angle less than
40 inches.
2
d2 Cv2
R2 =
1 – 1.5 1 -
D2 0.04d2
d = valve size mm. D = line size mm. Cv = required valve co-efficient.
To compensate for reducer
losses at sub-critical flow, divide Cv calculated by R.
113.
An operator tells you that a control valve in a stuck? How will you start
checking?
1. First of all get the control valve is passed
from operation.
2. Check the lingual to the diaphragm of the
control valve.
3. Disconnect it possible the actuator stem
from the control valve stem.
1.
Stroke the actuator and see whether the actuator
operates or not. It not then the
diaphragm may be punctured.
5. If the actuator operates connect it back to
the plug stem stroke the control valve. If it
does not operate loosen the gland nuts a
bit and see if it operates. If it does not then
the control valve has to be removed from
the line to w/shop.
114. Where is an Air to close and Air to open control valves used?
Air to close:
1. Reflux lines.
2. Cooling water lines.
3. Safety Relief services.
Air to open:
1. Feed lines.
2. Steam Service.
115. Why does control valve operate at I5 psi?
On higher pressure the
actuator sizes becomes bigger in area. The actual force produced by the
actuator.
Force = Pressure x
Area.
= 15 psi x Area,
If Area = 15"
Force produced = 15 psi x 25 in2 = 375 pounds.
Actual force acting on a control valve = 375 pounds.