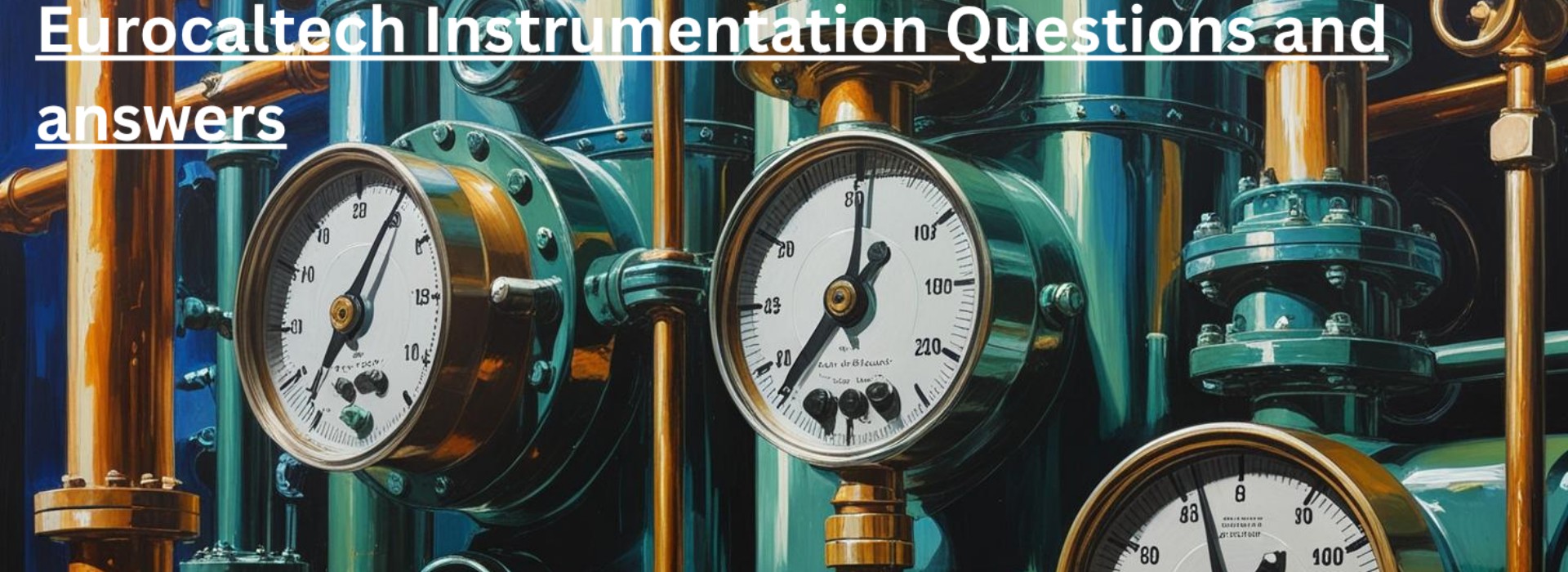
Instrumentation Interview questions and answers Control systems
CONTROL SYSTEMS
Explain the application of proportional integral and derivative action?
Proportional control only:
Proportional control only
attempts to return a measurement to the set point after a load upset has
occurred. How ever it is impossible for a proportional controller to return the
measurement exactly to the set point.
Use: It is normally
used for level controls. It reduces the effect of a load change but it cannot
eliminate it.
Proportional plus
reset (Integral) control:
Reset action is introduced to eliminate offset. It will integrate any
difference between measurement and set point and cause the controller's output
to change until the difference between the measurement and set point is zero.
Reset will act as long as the error exists.
Use: Proportional +
Reset controllers are by far the common types used in industrial process
control and where predominate dead times occur.
Proportional plus
reset plus derivative (Rate):
Derivative or rate action helps the controller overcome system inertia
and result in faster, more precise control. Derivative action occurs whenever
the measurement signal changes. Under study conditions the rate action does not
act. Derivative allows the controller to inject more corrective action.
Use: On temperature
controls.
67. What
is difference gap control? (On off control)
Differential gap control is
similar to on off control except that a band or gap exists around the control
point.
Use: In industry
differential gap control is often found in non-critical level control
applications where it is desirable only to prevent a tank from flooding or
drying. When a measured variable exceeds the upper gap the control valve
will open fully or be closed fully. Similarly when it exceeds the lower gap it
will open or close fully.
68. Where
is on off control used?
On off control is used when
1.
Precise control is not needed.
2.
Processes that have sufficient capacity to allow the
final operator to keep up with the measurement cycle.
3.
It is mainly used in refrigeration and is
conditioning systems.
69. What is reset-wind up?
When reset action is applied
in controllers where the measurement is away from the set point for long
periods the rest may drive the output to its maximum resulting in rest wind up.
When the process starts again the output will no come off its maximum until the
measurement crosses the so point causing large overshoots. This problem can be
avoided by including anti-reset wind up circuit, which eliminates the
problem of output saturation.
70. Why
is reset called integral and Rate derivative?
Reset is called integral
because of the mathematical relationship to the output.
Rate is called derivative
because
time
Oi = is the Output at any
given time
O0 = is the out
put at time zero or zero error.
e = is the error signal
t = is time.
f
= is the reset rate in respects per minute.
71. Explain
tuning of controllers.
Tuning basically involves
adjustment of proportional. Integral and derivative parameters to achieve good
control. The gain, time constants, and dead times around the loop will dictate
the settings of various parameters of the controller.
Tuning methods
are broadly classified into two:
1. Closed
2. Open Loop Method: e.g.
process Reaction curve.
Ultimate gain
method:
The term ultimate gain was attached to this method because their uses
require the determination of the ultimate gain (sensitivity) and ultimate
period. The ultimate sensitivity Ku is the maximum allowable value of gain (for
a controller with only Proportional mode) for which the system is stable. The
ultimate period is the period of the response with the gain set at its ultimate
value.
Process reaction
curve:
To deter mine the process reaction curve, the following steps are
recommended. :
1. Let the system come to steady state at the
normal load level.
2. Place the controller on manual.
3. Manually set the output of the controller at
the value at which it was operating in the automatic mode.
4. Allow the system to reach the steady state.
5. With controller on manual, impose a step
changes in the output of controller, which is an signal to value.
6. Record the response of controlled variable.
7. Return the controller output to its previous
value and return the controller to auto operation.
72. Explain
the working of an electronic P.I.D. controller.
Input from the measurement transmitter is compared with the set point
voltage to produce a deviation signal. The deviation signal is combined with a
characterized feed back signal to provide the input for the function generator
amplifier. This amplifiers output is delivered to the feed back network, and to
the final output which is a 10-50m.a. do signal for actuation of final
operators.